Supporting the rise of EV battery gigafactories
With electric vehicle sales poised to experience rapid growth globally, the demand for more gigafactories involved in EV battery production is rising. For major and emerging battery cell manufacturers looking to capitalize on this, support from an experienced logistics provider is key to success.
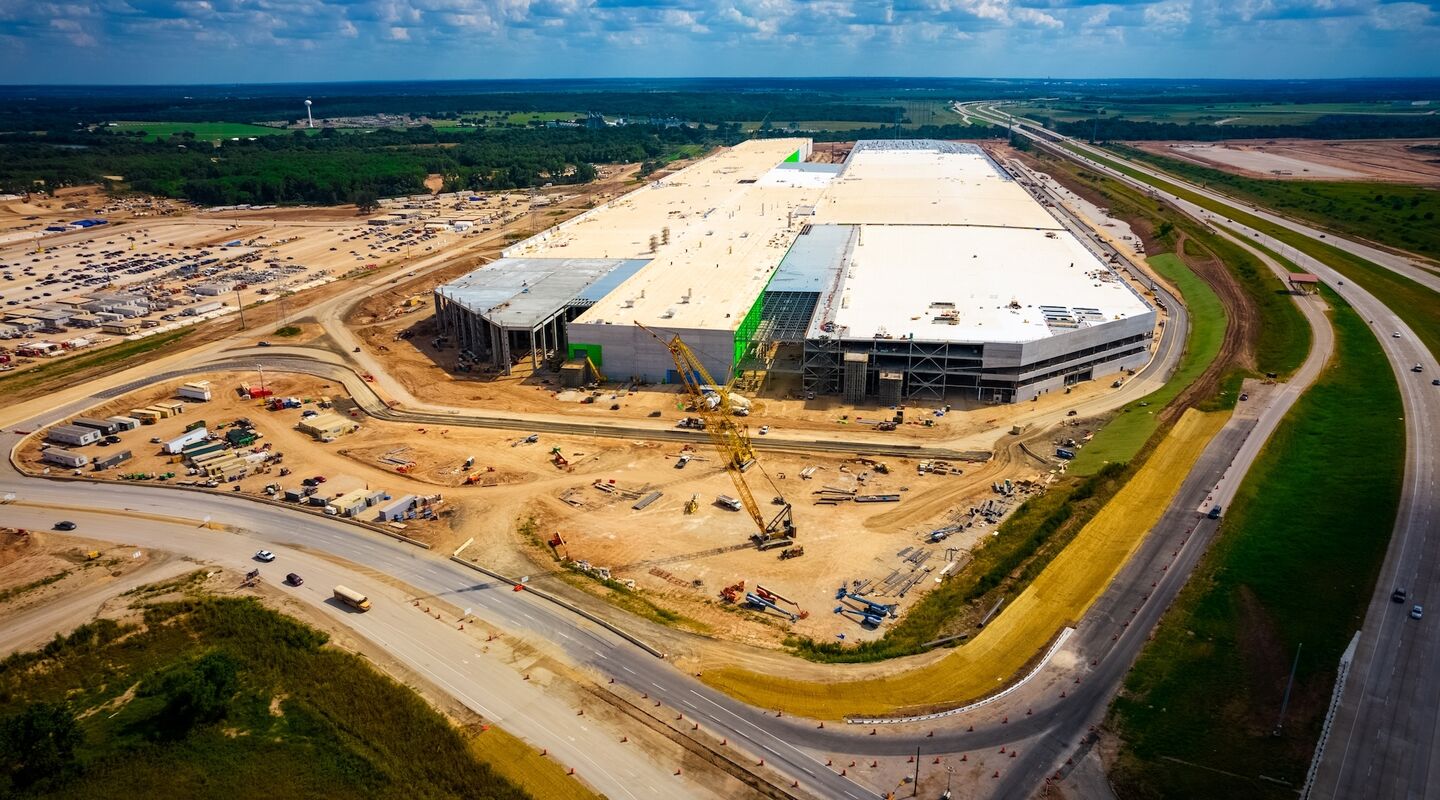
With the recent COP26 conference highlighting the need for reduction in emissions, big commitments were made towards all global sales of new cars and vans being zero emissions by 2040. This makes the potential growth of the already burgeoning electric vehicle market huge – the investment bank UBS forecasts that 40% of all new cars will be electric by 2030, rising to almost 100% by 2040. To achieve this, vehicle manufacturers, automotive suppliers and governments are plugging in more investment to regional supply chain and gigafactory networks for lithium-ion batteries.
With most of the world’s EV battery production currently in Asia, however, governments in Europe and North America see a need to develop their own battery production industry as a means of boosting EV adoption and simultaneously creating green jobs. In response, there is a boom in spending on EV battery gigafactories in these regions. With estimated investment in a gigafactory between £2 billion and £4 billion, these are significant construction enterprises relying on the timely and safe delivery of large equipment and machines.
"Building a gigafactory is a complicated process so organisations need the right partner to deliver the project on time, especially when facing global supply chain disruptions," says Hiroto Osonoi, business development manager, global industrial account development, Wallenius Wilhelmsen. "With established expertise in both breakbulk and automotive logistics, we are well equipped to support new battery start-ups and auto OEMs in this growing industry ."
Reliable ocean services ensure on-time delivery
As COVID-19 continues to impact on global business, the need for reliable logistics services becomes even more acute. Congestion at ports, especially in the Asia to Europe trade and in the US, makes finding shipping space a challenge.
Key to driving efficient and successful operations is predictability in both capacity and costs in the supply chain. While our network has also been impacted by market conditions, RoRo is more resilient in the face of these challenges and offers a stable solution for manufacturers and forwarders under pressure to meet tight project deadlines.
Building a gigafactory is a complicated process so organisations need the right partner to deliver the project on time, especially when facing global supply chain disruptionsbusiness development manager, global industrial account development
Safe handling minimizes the risk of damage
Regular sailings aside, the distinct advantage of our RoRo service is its fleet of specialized handling equipment, which removes the need for lifting to minimize the risk of damage not only during loading, but also during the sea voyage.
Our experience with transporting different types of breakbulk also means we have developed expert capabilities when it comes to cargo packing, which is critical to ensure the safe shipment of high-value products.
“All deep-sea transports require seaworthy cargo packaging to ensure safety during transport,” says Osonoi. “Our years of experience in handling different types of breakbulk means we can provide specialist support to customers, particularly those with little experience in preparing cargo packaging for export, and help them find ways to solve problems on-site.”
End-to-end sustainable logistics
Current attention is focused on EV battery production equipment – inbound logistics into the gigafactories – but as the industry matures, businesses will be looking at outbound logistics for end-products, such as energy battery storage systems."
There is a full-lifecycle logistics opportunity here; the world needs more batteries, but a plan for what to do after end-of-life has not had so much focus yet," says Osonoi. “By incorporating our Digital Accelerator program which adapts and combines technologies being used in other industries to support our business and offer more integrated logistics solutions to our customers, we can build an integrated end-to-end service to make a truly sustainable full lifecycle chain.”
With the supply and demand of electric vehicles set to dominate the future of the auto industry over the next 20 years, it’s now more important than ever that those in the industry find and work with the right logistics partners to be able to take on these challenges and find sustainable long-term solutions.
Gigafactory industry by numbers
- 38 : the number of EV battery gigafactories being built or planned in Europe in 2021
- 5: the number of operating gigafactories in USA in 2021
- 12: the number of gigafactories being built or planned in USA in 2021
- £2 billion-£4 billion: the cost of setting up a gigafactory
- 33.4%: the expected European share of global EV gigafactories (versus 8% in 2021)
- 69%: the global market share of the top three suppliers of batteries and battery metals in passenger EVS in H2 2020 (CATL, LG Energy Solution, Panasonic)